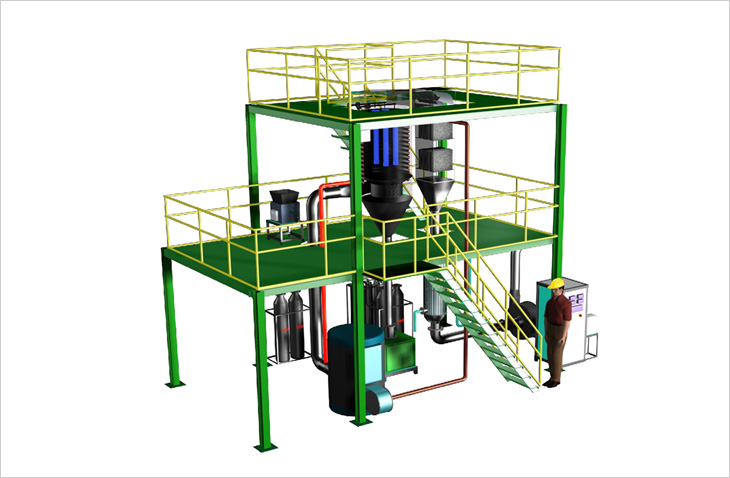

Fusion System for Handling Nanoparticles / Gaseous Matters As a compact fusion system, fine particles, acid gases (sulfur oxides), nitrogen oxides and the like present in gas fuels or combustion exhaust gases are effectively removed. Compared with the existing equipment, the cost and area can be reduced by 1/2 and 1/3 respectively.

- Due to the removal of sour gas, fine particles, and oxides of nitrogen along the exhaust flow direction on a single unit, costs and installation area are reduced by about ¨ö and 1/3, respectively, compared with existing equipment.
- Acid gas is effectively removed by injecting a highly reactive reagent into the front end and dispersing it uniformly. After the unreacted reactant is captured by the star-shaped ceramic filter attached to the fusion system, the removal reaction with acid gas is induced to occur twice, thereby increasing the removal rate of acid gas.
- By installing a multi-layer DeNOx chamber intended to fill a sealed catalyst at the rear end, the off-gas of acid gases and fine particles have been removed and will flow into the DeNOx chamber, thereby effectively removing nitrogen oxides.

A dust removal filter for gas purification, a filter for purification of exhaust gas in the manufacture of a catalyst, a filter for purification of exhaust gas in the production of chemicals, a filter for purification of exhaust gas in the dissolution of aluminum, High temperature high pressure fluidized bed combustion process for the purification of exhaust filters

- Power generation boilers, industrial boilers
- Gas turbines, waste incinerators
- Used for exhaust gas treatment and removal of nitrogen oxides from chemical plants, glass / steel / cement industries.

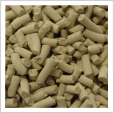
- Appearance & size: Pellet (¨ª=3.0 ¿Ü)
- Colour : light beige
- Bulk density : 0.73-0.75g/cc
- Crush strength : >1.0kg/cm2
- Recomm. operating temp. : 260~400¡É
- Upper temp. limit : < 400¡É

¹ÝÀÀ¸ÅÄ¿´ÏÁò
Gas |
Mechanism |
NOx |
4NO + 4NH3 + O2 ¡æ 4N2 + 6H2O |
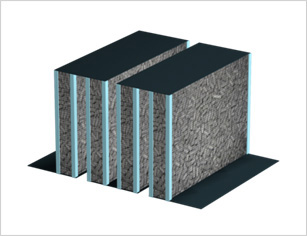

The high-strength particulate catalyst used for denitration is an oval granular catalyst with a large surface area so it can be easily installed according to the site conditions regardless of the location or structure of the installation site.At the same time, the surface strength of the catalyst can be enhanced from the shape characteristics of the catalyst, so that it is excellent in performance and also easy to recycle (recycle).

- Improve the durability of the denitration catalyst.
- Increase the amount of catalyst loading, catalyst regeneration (recycling) and adsorption / desorption.
- Increase the surface area of the catalyst to increase the reaction rate between the catalyst and nitrogen oxides.
- The use of catalyst packing chamber (filling chamber) molding technology, compared with existing equipment, the volume can be reduced by 70%.
- Easy catalyst regeneration (recycle) and adsorption / desorption reduce operating costs by up to 30% compared to existing equipment.
- Nitrogen oxide emissions in high temperature / pressure and exhaust gas combustion processes can be reduced to less than 10 ppm, keeping the surrounding environment clean.

- Catalysts and chambers for the removal of flue gas containing nitrogen oxides at sinter plants
- Catalysts and chambers for VOC removal in petrochemical plants
- Catalysts and chambers for gas purification in gas-fired combined cycle power plants
- Used in chemical plant N2O decomposition catalyst and chamber