High efficiency low temperature scr catalyst

Explanation
- Coating of high-efficiency, lightweight, stable and heat-resistant SCR catalyst material using excellent heat-resistant fiber.
- Boasting excellent SCR catalyst activity and dioxin removal performance with 3D pore structure and surface reaction of abundant technology
Distinction
- High efficiency: Unique TDP pore structure, reaction channel and pore active surface area construction, high dispersion of active ingredients, SCR reaction secured, SO2 oxidation suppression
- Light weight: Low density (volume density 30%) and light weight reduce usage (10%)
- Stability: Unique formula system satisfies various working environment requirements at low/medium/high temperatures
SCR reaction principle
.jpg)
.jpg)
Explanation
- Polluted air (NOx) moves to/is absorbed by the SCR catalyst and reacts with NOx first to be converted into N2 and H2O.
- O2 in the atmosphere forms a catalytic cycle through O transferred through the internal reaction of the catalyst.
SCR pore structure and performance
.jpg)
.jpg)
samples | BET Surface m©÷/g | BJH Surface m©÷/g | Pore Volume cm©ø/g | Average pore/Å |
---|---|---|---|---|
¹úÁýÇü SCR | 64.2 | 66.0 | 0.26 | 140 |
ÆÄÇü½Ä SCR | 114.0 | 114.5 | 0.31 | 99 |
SCR catalyst volume density
.jpg)
.jpg)
- The volume density is 35-43% lower compared to the corrugated and honeycomb catalysts.
SCR catalyst geometric surface area
.jpg)
.jpg)
The geometric surface area is +10% larger when comparing the corrugated and honeycomb catalysts.
Waveform SCR catalyst features
- The specialized 3D pore structure forms large/medium/small pores and promotes rapid diffusion to maximize catalytic activity.
- The high-efficiency catalyst is coated on the high-temperature fiber structure, which has a higher volume density and is more resistant to thermal shock than the honeycomb catalyst.
- The corrugated structure, which provides a high active surface area with uniform pore walls, promotes the SCR reaction and suppresses SO2 oxidation.
Advantages
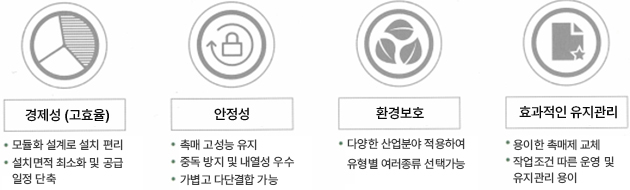
Catalytic performance

.jpg)
.jpg)
Gas turbine combustion gas denitrification efficiency
- Inlet nox : 150~250 mg/Nm3
- Outlet nox : ¡Â50 mg/Nm3
- Exhaust temperature : 300~350¡É

.jpg)
.jpg)
Steel mill combustion gas denitrification efficiency
- Inlet nox : 70~90 mg/Nm3
- Outlet nox : ¡Â20 mg/Nm3
- Exhaust temperature : 145~150¡É

.jpg)
.jpg)
Waste combustion gas denitrification efficiency
- Inlet nox : 200~250 mg/Nm3
- Outlet nox : ¡Â80 mg/Nm3
- Exhaust temperature : 180~230¡É

.jpg)
.jpg)
Petrochemicals combustion gas denitrification efficiency
- Inlet nox : 150~200 mg/Nm3
- Outlet nox : ¡Â50 mg/Nm3
- Exhaust temperature : 230~240¡É

.jpg)
.jpg)
Internal combustion engine combustion gas denitrification efficiency
- Inlet nox : 500~3500 mg/Nm3
- Outlet nox : ¡Â50 mg/Nm3
- Exhaust temperature : 350~380¡É, 500~550¡É

.jpg)
.jpg)
Marine engine combustion gas denitrification efficiency
- Inlet nox : 9.8 g/KW.h
- Outlet nox : ¡Â1.5 g/KW.h
- Exhaust temperature : 280~400¡É
Standard
.jpg)
.jpg)
.jpg)
.jpg)
±Ô°Ý | ±â°øº® µÎ²²mm | ±â°øÀ² % | ±â°ø¹Ðµµ CPSI | ±âÇϺñÇ¥¸éÀû m©÷/m©ø | üÀû¹Ðµµ kg/m©ø |
---|---|---|---|---|---|
NDC-16 | 0.3 | 73% | 179 | 1838 | 310 |
NDC-22 | 0.3 | 74% | 123 | 1505 | 310 |
NDC-27 | 0.3 | 78% | 65 | 1190 | 290 |
NDC-33 | 0.3 | 80% | 46 | 992 | 280 |
NDC-42 | 0.4 | 80% | 33 | 839 | 280 |
NDC-51 | 0.5 | 81% | 22 | 745 | 270 |
NDC-56 | 0.5 | 82% | 20 | 634 | 270 |
Application areas

SITE MAP
-
Company Introduction
-
Business field
-
C&G Result
-
Customer