All-in-one VOCs Adsorption for removal and Concentration regeneration device
Introduction of the facility
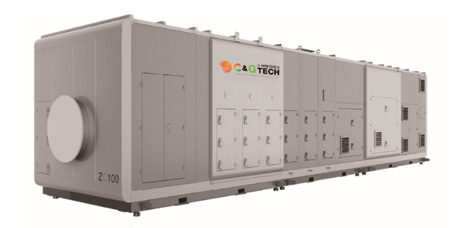
Distinction
- Apply modular design
- Easy to disassemble and assemble
- Assembly with different functional modules
- Select and assemble each functional module according to the field situation
Process
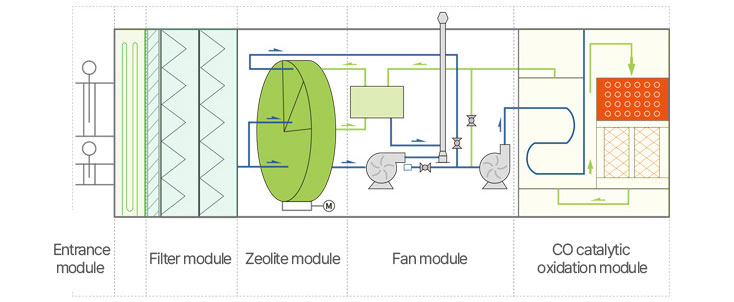
Adsorption/Concentration technology combination system
VOCs adsorption concentration rotary ROTOR and catalytic oxidation CO combined VOCs management system
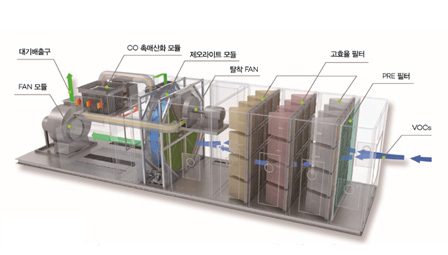
Distinction
- Oxidation temperature 300¡ÆC
- Using tube or plate heat exchanger, heat efficiency 65%
- Processing efficiency 90% ~ 99%
- Land area is relatively small
- Maximum internal temperature ~500¡ÆC
- Suitable for intermittent operation
- Cannot process organic substances such as sulfur and halogen
VOCs adsorption concentration turntable
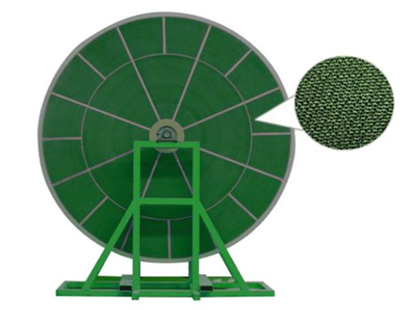
Distinction
- Excellent adsorption performance
- Adsorption efficiency 90 ~ 99%
- Available in various shapes
Catalytic oxidation
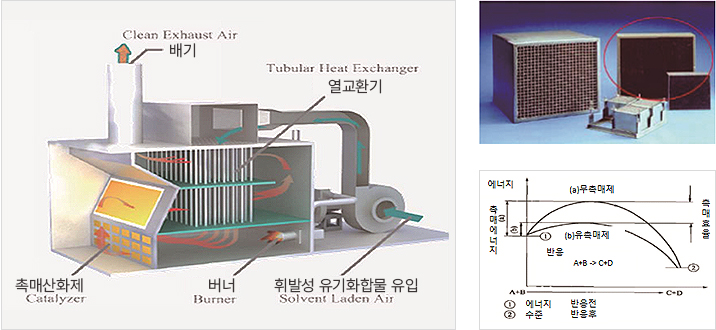
Distinction
- The catalytic action reduces fuel consumption by lowering the activation energy of the reaction during the catalytic combustion process.
- Catalytic oxidation heats the exhaust gas to 300¡É and completely decomposes organic matter into CO©ü and H2O through the catalytic action.
- Using precious metal (Pt, Pd) catalysts, energy consumption is reduced due to low reaction temperature, and the purification efficiency is over 95%, which reduces investment costs.
- Using a ceramic carrier stabilized at high temperatures, the catalyst does not sinter, and maintains a large specific surface area, mechanical strength, and stability against high heat.
Technical Advantages of catalysts
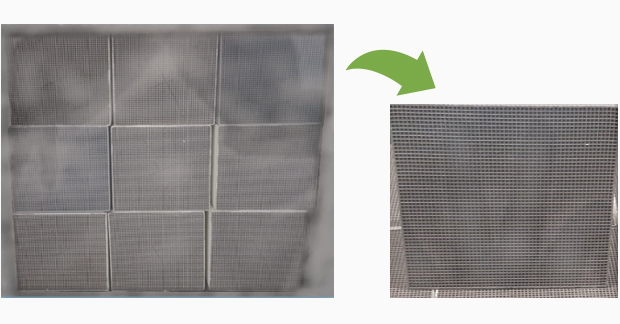
Distinction
- 40~50% weight reduction compared to existing products
- 30% increase in surface area due to high porosity
- Reliable low-temperature and high-temperature catalytic activity
- Increased diameter, increased treatment area
Operating costs and energy consumption
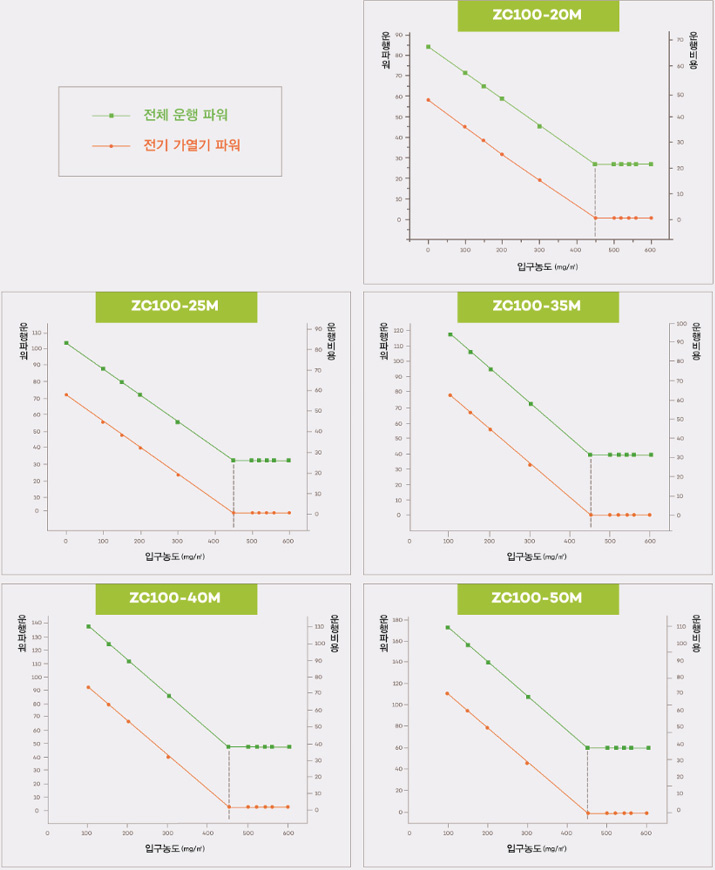
Test report
1. Adsorption test
½ÃÇè Ç׸ñ ¹× Á¶°Ç
VOCsÀ¯Çü | dz·® m©ø/h | ³óµµ ppm | Ãⱸ³óµµ | |
---|---|---|---|---|
½ÇÇè 1 | ÀÚÀÏ·» | 20000 | 300-400 | < 30 |
½ÇÇè 2 | ÀÚÀÏ·»-¾ÆÅھƼ¼Å×ÀÌÆ® (2:1) | 20000 | 300-400 | < 30 |
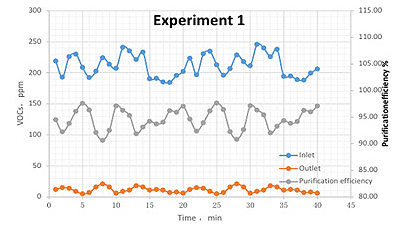
Result
As can be seen in the exhaust gas concentration graph, the xylene inlet concentration is 190~330ppm, the exhaust gas emission concentration is 5~10ppm, and the overall equipment efficiency is over 92%.
2. Desorption test
½ÃÇè Ç׸ñ ¹× Á¶°Ç
VOCsÀ¯Çü | dz·® m©ø/h | ³óµµ ppm | Å»ÂøÇ³·® Nm©ø/h | ºÐÀÚ ·ÎŸÀ¯Çü | |
---|---|---|---|---|---|
½ÇÇè 1 | ÀÚÀÏ·» | 20000 | 200-330 | 2500 | 2350-40-III |
½ÇÇè 2 | ÀÚÀÏ·»-¾ÆÅھƼ¼Å×ÀÌÆ® (2:1) | 20000 | 200-400 | 2500 |
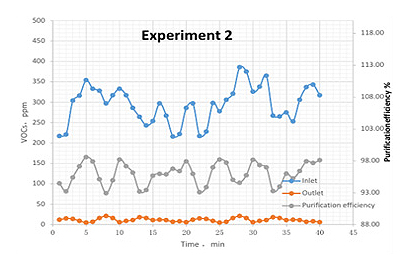
Result
As can be seen in the exhaust gas concentration graph (xylene: ethyl acetate = 2:1), the inlet concentration is 200 to 400 ppm, the exhaust gas outlet concentration is 5 to 20 ppm, and the overall efficiency of the equipment is over 93%.